Rethinking Bhopal- A Process Safety Analysis of the Union Carbide Bhopal Plant
A comprehensive examination of the important technical elements of the Bhopal Gas Tragedy by Kenneth Bloch
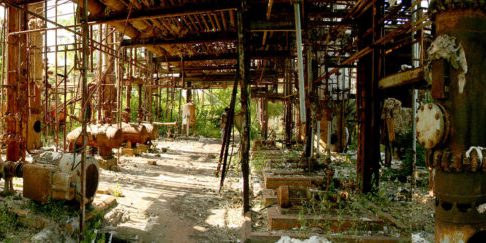
Rethinking Bhopal- A Process Safety Analysis of the Union Carbide Bhopal Plant
A comprehensive examination of the important technical elements of the Bhopal Gas Tragedy by Kenneth Bloch
Author of ‘Rethinking Bhopal’, Kenneth Bloch, is a process safety professional who has taken a very deep interest in the Bhopal Disaster story.
Rethinking Bhopal is a meticulously researched account of history’s worst single-incident industrial disaster. It contextualises the process facts of the Bhopal plant, comparing them to accepted norms, and presents them in a relatively easily-digestible format. A major aim of Rethinking Bhopal is not just to produce a historical account of one terrible disaster but to engender better thinking and practice within industry professionals operating today.
Kenneth Bloch has now put together, for our benefit, a comprehensive examination of the important technical elements of the Bhopal Gas Tragedy:
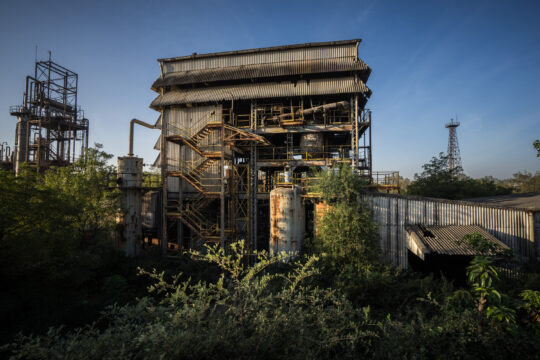
The Bhopal Gas Tragedy drove improvements that made industry safer. By protecting the lives of others, industry now honors those whose lives were suddenly changed on December 3, 1984 – some of whom may read this blog regularly.
Among these are survivors who lost their health, family, or friends. Also included are workers and others who designed, operated, and maintained the equipment that became hostile. Like parents of a rebellious child that was raised and nurtured with love, care, and affection to be a productive member of society, their unjust sense of hindsight must be unbearable. My heart goes out to all of you.
Methyl Isocyanate (MIC) Rundown & Storage System
The series begins with a Process Flow Diagram (PFD) of the MIC Storage System that was involved in the Bhopal Gas Tragedy.
The drawing is “As-Built,” which means that it shows the system as it appeared upon placing it in service. The PFD reveals how the process was both remarkably efficient and vulnerable.
When reviewing the PFD, pay close attention to (1) using carbon carbon steel for all equipment in MIC vapor service, (2) the need for a clear, open, unobstructed path between the E-210 MRS and the E-408 VGS atmospheric vent, and (3) nitrogen injection into the E-610, E-611, and E-619 tank head manifolds.
An unbreakable dependency was formed between these three items, which made it impossible to change one without impacting the others. The dependency was rooted in deviating from a design standard that prohibited the use of carbon steel for equipment in MIC service.
Adherence to the design standard would have resulted in the use of stainless steel in MIC vapor service, where carbon steel was used. MIC polymerizes upon contacting rust; thus, a rust-resistant material such as stainless steel was needed to avoid incompatibility complications. Why was carbon steel, which would rust upon contact with air, used instead? To save money by reducing construction costs.
Saving money is something that most people can relate to. Most people must learn to survive on limited resources that prevent us from spending more money than we make. The same is true for any company that expects to stay in business. Companies that spend more money than they generate will eventually go out of business.
Looking at the PFD, it becomes clear that the system was designed to operate under a continuous nitrogen purge starting at the storage tank heads and terminating upon its discharge through the VGS atmospheric vent. Stainless steel resists rust, but nitrogen in this case does the same thing by eliminating oxygen (air) that carbon steel needs to rust.
The purpose for nitrogen was to eliminate air that could allow MIC in the storage tanks to ignite. It also served as a corrosion inhibitor for carbon steel equipment found in MIC vapor service by preventing air from migrating into the system through the atmospheric vent.
When I look at the drawing I see an efficient, compact, and reliable process design. On paper, everything works perfectly. But although perfection is the goal we all work toward, nothing could be further from our reach when operating a typical industrial process.
Major Safety Concerns Listed in September 11, 1984 Report
A different kind of “911” happened in 1984. September 11, 1984 was the date that Union Carbide management received the results of an “Operational Safety/Health Survey” completed at the Institute Methyl Isocyanate (MIC) Unit in West Virginia (now Bayer CropScience).
Factory blueprints from that existing process were used to construct the pesticide factory where the Bhopal Gas Tragedy occurred.
More specifically, the report describes a scenario where cooling water leakage from the MRS Condenser could initiate a runaway reaction inside the MIC storage tanks. Less than three months after the audit report was submitted, a runaway reaction initiated by water leaking into an MIC storage tank did occur at the Bhopal factory. The report noted a history of cooling water contamination by this route in the past, with less severe consequences. The first part of this technical series shows how this could happen through the “MIC Rundown” line that connected the MRS Condenser to the MIC Storage Tanks, at the bottom left of the PFD.
Before proceeding, let’s all agree that hindsight is always 20/20. Trevor Kletz stated it best by referring to not knowing what you don’t know. With Trevor’s thought in mind, is it fair to criticize someone for not having the knowledge they needed to prevent an incident? Is there a difference when someone possesses the knowledge needed to prevent an incident, but fails to act upon it? Think about it.
The Bhopal Gas Tragedy forced industry to implement practices to identify, evaluate, and address process hazards like the one described in the September 11, 1984 audit report. The analysis provided in Part 2 of this technical series did not exist before the Bhopal Gas Tragedy. Like buckling one’s seatbelt upon getting into an automobile, this safety practice is so routine now that we would never think about not doing it. Things were much different back in 1984 when the concepts demonstrated here were immature at best, and not uniformly practiced globally. But if this practice was mandatory prior to 1984, would it have prevented the Bhopal Gas Tragedy?
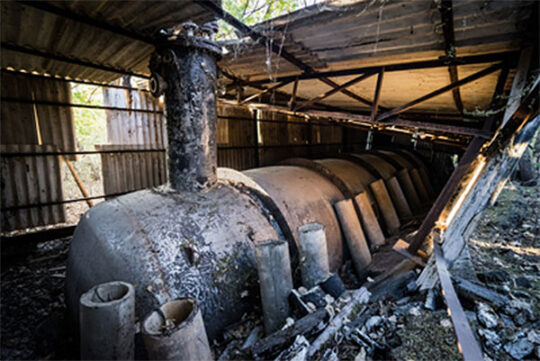
Answering that question requires that adequate safeguards exist to realistically prevent an MIC gas release if water was to contaminate MIC in a storage tank. Many of the safeguards used to prevent this kind of incident can be observed in the PFD provided in the first part of this series. They were described by Ron Van Mynen, Union Carbide’s Corporate Director of Health and Safety, in a press conference on March 20, 1985 as:
- A 30-ton refrigeration system to keep the MIC at a low temperature (0 ⚬C)
- A temperature alarm activated by high temperature (11 ⚬C)
- Daily MIC storage tank sample testing by operators trained to implement process isolation procedure upon obtaining evidence of contamination
- A versatile arrangement of pipes and valves to reprocess or destroy the contaminated material
- An empty storage tank (E-619) to contain the contaminated material and provide additional vapor space and cooling if a runaway reaction was to occur
- A Vent Gas Scrubber (VGS) to destroy MIC through contact with a circulating stream of caustic material (sodium hydroxide)
- A flare tower to be used as a last resort by burning-off any material making it all the way past the VGS.
On the surface, there appear to be more than enough safeguards to prevent a toxic gas release resulting from a runaway reaction inside the storage tank. However, a much different conclusion is reached by using a method that was introduced in 2001 that assigns a credit (point) value to each of the safeguards. This “Layer of Protection Analysis” (LOPA) method operates on the basic premises that (1) no safeguard is 100% perfect, or always “available,” and (2) a safeguard must be independent (an Independent Protective Layer or IPL) for any additional credit to be taken.
Unfortunately, the tight-coupling of dependencies mentioned in the first installment of this series defeats essentially all of the safeguards provided in the MIC Rundown and Storage system. The graphic shows how.
For example, we might accept 1/10 credit for the 30-ton refrigeration system under the assumption that well-maintained mechanical equipment can be expected to fail once every ten years. However, looking at the drawing we see that the refrigeration system operates on discharge from the MIC Circulation Pump. If this pump fails, then the refrigeration system becomes useless (a “Common Mode Failure”). The refrigeration system is therefore dependent on Circulation pump reliability.
To complicate matters further, the high temperature alarm is dependent on refrigeration system operation, which again is dependent on MIC Circulation Pump reliability. In other words, if the MIC Circulation Pump fails then not only is the refrigeration system lost, but also the ability to detect a high temperature condition created by a thermal runaway reaction because the alarm is already active and probably disabled or ignored until the pump is repaired. In this context, the high temperature alarm serves only as a nonspecific “common trouble” alarm that can be activated either by a mechanical or process failure.
Finally, if the Circulation Pump fails then the drawing shows that access to the reject line is also lost. Under these circumstances, MIC storage tank contents cannot be directed into the VGS, the empty reject storage tank, the other uncontaminated tank, or the return line back to the MIC manufacturing unit for reprocessing. None of those safeguards exist.
Furthermore, “double jeopardy” does not apply in this situation because even though the logic operating here requires two independent failures (MRS Condenser leakage and a Circulation Pump failure), only one failure is detectable at a time. In this scenario either a Circulation Pump failure or contamination incident activates the high-temperature alarm and no other independent indicator is available for the other condition, such as a high-pressure alarm.
A circulation pump failure would consume the only early indicator of a continuous contamination incident, meaning that a contamination incident could progress to a very late stage before an unexpected, undeniable system response would signal a problem. In the context of the Bhopal Gas Tragedy, these circumstances sound very familiar.
Part 3 of The Bhopal Gas Tragedy Technical Series will examine the consequences of MIC pump failures at the Bhopal plant, which in reality occurred multiple times per year. For that reason, the LOPA analysis accurately ends with no credit taken for the 1 in 1 year (1/1) actual probability of a Circulation Pump failure. Factoring actual Circulation Pump reliability into the analysis creates a highly-probable proposed scenario, with 1 predicted occurrence in the first 10 years of operation. Coincidentally, a similar incident happened five years into operation at the Bhopal factory.
Most companies that use the LOPA method require a frequency far less than 1/10 (one in ten years) for a toxic chemical release with potential widespread community impact – say 1/10,000,000 or a one in ten-million-year frequency. Anything higher would require a redesign for a system not yet constructed. For systems in service with a gulf so huge between actual and acceptable, an immediate shutdown would follow.
Points to Remember
Hindsight is 20/20 and things unseen are readily apparent after they occur. An analysis with the level of depth demonstrated on the MIC Rundown and Storage system is probably not possible without “hindsight bias.” But this is why we investigate an incident after it occurs – to replace the things we missed with things we learn. In doing so, may we continue to learn how to avoid incidents that we cannot afford to repeat, and continue to extract value from incidents with tragic consequences.
Many significant incident investigations finish after determining what happened. However, knowing why the incident happened is infinitely more important. Unfortunately, this is where most incident investigation reports fail. They describe only what happened without explaining why it happened.
Simply knowing what happened makes it difficult to prevent future problems. In other words, adding value requires knowing why the incident happened. Only then can we picture how we might react to the same situation when things start brewing again. But determining why an incident happened usually requires looking deep beneath the surface of what happened. Sometimes it exposes something that changes our perception about what happened.
The Bhopal Gas Tragedy is a perfect example that supports this fact. Union Carbide’s website that covers the Bhopal Gas Tragedy provides access to an independent investigation report issued by Arthur D. Little (ADL). This report contains trustworthy information about the incident. Indeed, the ADL report offers a credible, scientific basis behind what happened. But does the report accurately reflect why the incident happened?
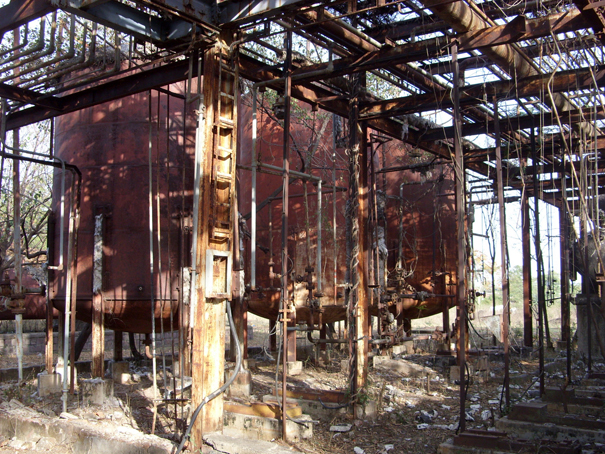
Settling Differences
To answer that question, let’s consider how the completeness of a formal incident investigation report might be assessed. For one thing, one might expect the final investigation report to contain no technical inconsistencies.
Disparities that are not thoroughly explained ultimately lead to conjecture and controversy. This could unfairly undermine the credibility of an otherwise good investigation report, and the investigation team’s effort behind it. Therefore, a final investigation report carefully documents how technical differences between one or more credible references were resolved. Never should a final investigation report fail to meet this basic expectation for acceptance, especially in cases involving severe consequences.
Specific information contained in the ADL report conflicts with a system diagram that was published in Union Carbide’s official internal investigation report. In this way the ADL report does not satisfy a basic requirement for an acceptable final investigation report. The conflicting references are both considered credible, since they originated from a common source (Union Carbide).
In the ADL report we read: “The MIC was transferred in one-ton batches to a charge pot in the SEVIN unit using nitrogen pressure. A nitrogen pressure of at least 14 PSIG in the MIC storage tank was necessary to move the material from the storage area to the SEVIN unit charge pot at a reasonable rate.”
This technical description contradicts information in the tank diagram that shows a “transfer pump” attached to the MIC storage tank. If a MIC transfer pump existed as indicated on the tank drawing, then there was no need to establish a minimum pressure of 14 PSIG inside the MIC storage tank as stated in the ADL report. The transfer pump would have delivered MIC into the pesticide production area (MIC Derivatives) without difficulty, regardless of the storage tank pressure.
Prematurely jumping to conclusions can hamper an otherwise good investigation. This inconsistency simply means that the documentation in the ADL report is incomplete. The significance of any disparity detected during an incident investigation is unknown until it has been completely examined. Closing the information gap requires poking beneath the surface of what happened. Digging deeper to reconcile the inconsistency may yield more insight into why the Bhopal Gas Tragedy happened.
Gap Closure
The photograph appearing at the top of this article contains visible evidence that the MIC transfer pumps were installed during original factory construction.
Notice the five small concrete pump pedestals at the bottom-right of the photo, in the space between the MIC and solvent storage tanks. At the time of the incident on December 3, 1984 these pumps were not being used.
This third installment of the Bhopal Gas Tragedy Technical Series (click on the graphic above to download the pdf file) covers the significance of this intentional change in operating methodology. The top line (boxes 1 through 3) simulates how the system was expected to perform under design conditions when the factory was commissioned with MIC transfer pumps. The MIC storage tank vent valves were always open, allowing nitrogen to continuously contact the iron components in MIC vapor service.
This type of operation was simple, clean, and efficient. Pipes and valves in MIC vapor service remained free from rust and debris. There was no need to clean them routinely, in between major maintenance intervals. The decision to save money by constructing system components in MIC vapor service with iron instead of stainless steel was inconsequential. Pesticide production meeting quality specifications (less than 0.5% chloroform solvent) was possible whether the tank was being filled with MIC from the MIC Refining Still (MRS) or not.
Abandoning the transfer pumps required closing the MIC storage tank vent valves. Boxes 4 through 9 simulate how the system responded to this substitute operating procedure. Closing the vent valves isolated nitrogen from the pipes and valves in MIC vapor service, and allowed air containing oxygen to migrate into the VGS.
This action was needed to bypass the MIC transfer pumps; making it possible to send tank contents into MIC Derivatives using differential pressure as documented in the ADL report. However, oxygen now infiltrating the system contacted the iron pipes and valves in MIC vapor service. Replacing nitrogen with oxygen resulted in internal corrosion, which produced rust. This rust catalyzed MIC “trimer” formation on iron components when the vent valves were reopened during tank filling. Trimer deposits accumulated inside the PVH, which restricted vapor flow to the VGS while filling the MIC storage tanks. Backpressure on the MRS, caused by restricted vapor flow through the PVH, resulted in MRS flooding – meaning that the MRS tower started retaining more liquid.
In response to MRS tower flooding, the temperature inside the MRS was raised to increase evaporation and send more liquid out of the tower. Unfortunately, this elevated the chloroform solvent level in the distilled MIC rundown stream. Eventually, the chloroform content inside the MIC storage tank exceeded the 0.5% maximum quality limit. Contaminated MIC exceeding the chloroform limit would then have to be reprocessed, recovered, or destroyed at great expense. Lost production due to business interruption during this period made it difficult for the factory to compete with other suppliers that were able to remain online.
Installing a flex-hose jumper to connect the trimer-choked PVH to the corroded, but clean, Relief Valve Vent Header (RVVH) offered an immediate, albeit short-term, solution. This action temporarily restored the production of MIC that met the purity limit but transferred the trimer accumulation problem into the RVVH. When both vent headers were choked with trimer, making it impossible to produce MIC meeting quality specifications, the system was shut down for cleaning.
Acceptable system performance was temporarily restored by flushing trimer from the lines with water. Since the system was not equipped by design for this type of alternative maintenance procedure, improvisation was necessary. Water hoses were attached by replacing threaded pressure gauges with adapters at various locations along the vent header system. Water was then introduced to the system to flush the vent header lines; clearing them of trimer deposits restricting vapor traffic. When the iron components in MIC vapor service were clean, the system was put back into service and the cycle repeated as trimer continued to build-up on corroded internal iron surfaces.
The Big Picture
The information yielded by examining the inconsistency preserved in the ADL report is extraordinarily significant.
This insight exposes how the choices we make prior to constructing an industrial process can end-up being counterproductive, depending on how a system changes during its life cycle. This specific example explains why water, a known MIC contaminant capable of causing an adverse and dangerous reaction, was routinely injected into MIC process piping. We have learned that this was not the design intent for the original system. In fact, trimer fouling in MIC vapor service that necessitated the routine invasive use of water would have been nonexistent if the system had been in conformance with the stainless steel design standard. Likewise, routine water flushing would not have been necessary if the MIC transfer pumps had not been bypassed.
This analysis in no way invalidates the ADL report’s determination about what happened. It does, however, provide the missing information needed to understand why the incident happened. Over three decades of employment in the manufacturing industry has given me the opportunity to investigate hundreds of industrial incidents; some of which were highly consequential. As others with similar experience know, there is no “honor among thieves” between operators, workers, or Union Brothers. If someone mischievously compromises the process to deliberately cause a system malfunction, their coworkers will find out who did it and immediately rat them out. The insight gained by reconciling the unaddressed inconsistency in the ADL report provides something I can relate to. It gives me something to recognize that I am constantly exposed to when working in a manufacturing environment. It also aligns more closely with the input of eyewitnesses who were inside the factory when the incident occurred.
If all of this unnecessary work, complexity, and risk could have been avoided by simply using the transfer pumps according to the original system design, why were the MIC transfer pumps abandoned? Reliable sources cited in Rethinking Bhopal (ISBN 978012803778) indicate the MIC transfer pumps were not reliable. In fact, the MIC pump seals leaked at an average rate of about once every 24 days per pump. MIC is a highly-toxic substance that could not be safely released into the atmosphere. MIC pump seal failures created an exposure hazard. Additionally, damaged transfer pumps were removed from service for repair. Recurring pump maintenance was costly and resulted in loss of commodity market share. An alternative, more reliable MIC transfer method offered a solution even though it added considerable complexity, effort, cost, and risk.
Some readers may reject this explanation on the basis that an MIC circulation pump also existed. The MIC storage tank drawing shows that the circulation pump processed tank contents through a refrigeration unit. The circulation pump suction and discharge lines originated and terminated at the same places as the transfer pump. The pump pedestal photo at the beginning of this article suggests that these pumps were identical. Therefore, if the transfer pumps suffered from poor reliability, then similar problems would likely have impacted the circulation pumps also. Under these circumstances it would have been difficult to keep the refrigeration system operating, and there is no evidence to support this conclusion . . .
. . . or is there?
Note to Self
Telling what happened involves explaining why it happened.
The countdown was in progress. Just 5 more months remained before the problem would correct itself. That is when January 1, 1985 would arrive. The Bhopal Factory’s operating license would then expire. At that point the inventor would move a safe distance away from a relationship that became the epicenter of an unprecedented financial disaster.
Both parties had conceded defeat. There was no interest in renewing the operating license. The factory’s fate would resemble countless other failed business experiments that time eventually erases from memory. January 1, 1985 would mark the sad but safe ending to an economic nightmare that began with a dream for independent pesticide production.
Three months earlier, factory production suddenly stopped. In hindsight, this unforeseen occurrence should have been expected after disillusioned investors withdrew their financial support earlier in the year. Funds needed to continue subsidizing the factory’s excessive maintenance load soon ran out, but operators were prepared to handle the crisis. They had been professionally-trained in the art of making creative use of reality. Without adequate maintenance department staffing, the operators temporarily kept things running with parts scavenged from adjunct equipment. This destructive approach to business continuity only accelerated the factory’s premature shutdown.
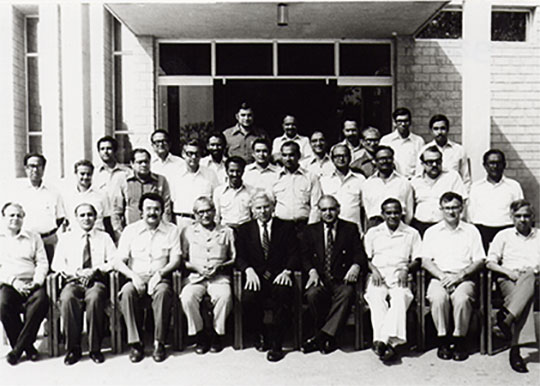
Like a disobedient child, the rebellious factory was finally receiving a dose of well-deserved discipline. Since its birth it had never met performance expectations, by not offering its investors a financial return. Cornered in a figurative “time-out” period, the factory could do no harm for the next 5 months. Sadly, no behavioural, or in this case reliability, improvement would be demonstrated upon its emergence on January 1, 1985.
At that time the lifeless and abandoned factory would silently pass into anonymity.
Intervention
The factory’s premature shutdown left an itch that became increasingly harder not to scratch.
An abundance of raw materials remained on-site. Safely concealed in the factory’s chemical storage area, these products were neither a safety nor environmental threat. Five months later, their loss would be absorbed in the write-off of a factory already deep in debt.
However, these raw materials were purchased with no intention of shutting down production before the operating license expired. Five months of watching useful chemicals stagnate to a wasteful end seem like an eternity. The “do nothing” option was no part of the inventor’s formula for success that involved making creative use of reality.
Perhaps the raw materials could somehow be converted into final pesticide product before January 1, 1985. If so, might that make some economic relief possible? No, this option was unthinkable with the factory in its hopeless state of disrepair! Neither was there enough time to resume production even if the system could somehow be resurrected. Or was 5 months enough time? Did enough time exist for a final production run to deplete the excess raw material inventory while generating some income to offset the approaching financial pain?
Although watching chemicals stagnate for 5 months seems like an eternity, recommissioning a disassembled chemical manufacturing operation within 5 months requires time travel. If this option was to be exercised, there was no time to waste. Things would have to get done at the speed of light.
Liquidation Plan
A liquidation plan was immediately developed. Factory production would commence in the simplest of terms to save both time and money.
Personnel on the battery factory’s payroll would staff nonstop chemical plant production. Manufacturing would begin immediately after sufficient repairs were completed, starting with methylisocyanate (C2H3NO), or “MIC,” production.
A modified MIC storage tank operating procedure was introduced to make creative use of the reality that vital process equipment had been disassembled. Normal operation involved running the two MIC storage tanks (Tank E610 and Tank E611) independently; each having its own dedicated rundown line and circulation pump. Reconfiguring the MIC storage tanks to operate in a “Parent-Child” relationship made it possible to return both tanks to service after restoring only one MIC circulation pump and rundown line.
The modified operating procedure directed MIC rundown from the MIC Refining Still (MRS) exclusively into Tank E610 for the duration of MIC production. Tank E610 would thereby serve as the “parent” tank, equipped with the working MIC circulation pump and rundown line. The MIC circulation pump would provide access to the “child” MIC storage tank (Tank E611) through the reject line. It was also required to chill the tank contents while filling the parent tank, as specified in standard operating procedures.
MIC production would continue until either (1) the remaining inventory of raw materials was completely consumed, or (2) both MIC storage tanks were full (whichever came first). Upon either event, the MIC process would be shut down permanently. The contents of MIC Storage Tanks E610 and E611 would then continuously be reacted into final product to be sold on the open market. The nonstop production campaign would end only upon consuming the MIC inventory or at the stroke of midnight between December 31, 1984 and January 1, 1985 (again, whichever came first). Any unreacted chemicals remaining on January 1, 1985 would have to be disposed by alternative, destructive, and costly means.
Limited Restart
By October 7, 1984 enough process functionality had been restored to start MIC production into Tank E610.
The system was returned to service upon opening Tank E610’s vent valve. This valve was left open to continuously route displaced tank headspace vapors into the Vent Gas Scrubber (VGS) as MIC ran down into Tank E610.
Tank E610 reached its maximum level (full) on October 18, 1984. According to the liquidation plan, its contents were transferred to Tank E611. This operation took place by opening Tank E611’s vent valve and using the circulation pump to top-off Tank E611 with MIC through Tank E610’s reject line. When the transfer was complete, Tank E611’s vent valve was closed. Nitrogen was then added to Tank E611 to establish 14 PSIG pressure and MIC production into Tank E610 continued.
Repeat Failure
The next day, Tank E610’s circulation pump seal leaked. This development was anticipated, since MIC pump seal failures were common throughout the Bhopal factory’s short life. At no prior time in the factory’s history had an MIC pump seal survived more than a month of continuous operation.
From a functional perspective, the MIC circulation pump failure was inconsequential to filling the child MIC storage tank, E611. That function had been performed successfully on the previous day. However, standard operating procedures specified that MIC refrigeration was required upon opening the vent valve to fill a tank. The refrigeration function failed without MIC circulation. Therefore, continuing MIC production without a working circulation pump deviated from standard (albeit modified) operating procedures governing MIC storage tank operation. But the liquidation plan stated that MIC production would cease upon (1) consuming the remaining raw material inventory, or (2) filling both MIC storage tanks to capacity. Since neither of these conditions had been met, the circulation pump was isolated to stop the leak and MIC production into Tank E610 continued.
MIC rundown into Tank E610 continued without refrigeration until October 22, 1984 when both MIC storage tanks were completely full. At that point MIC production was stopped in accordance with the liquidation plan. Tank E610’s vent valve was then closed and the VGS was shut down. Both tanks now contained about 42 tons of MIC, each.
System Fouling
The loss of the circulation pump increased the presence of MIC vapor in the iron Process Vent Header (PVH) piping system.
Unknown to the operators, this accelerated the rate of polymerized MIC (C6H9N3O3), or “trimer,” deposit formation inside the PVH pipe walls and valves. The internal deposit build-up was severe enough to choke PVH vapor flow. The resulting MRS backpressure caused a process upset that contaminated the MIC batch in Tank E610. Chloroform exceeded the maximum quality specification of 0.5 percent inside Tank E610 at the end of the MIC production run due to this process upset. This contamination event also went undetected since the circulation pump failure interrupted MIC tank sample flow.
The trimer build-up inside the PVH that affected MIC product quality was excessive. In fact, its large volume impacted Tank E610’s iron vent valve. Trimer deposits that formed inside the vent valve while it was open made it impossible to isolate Tank E610 from the PVH when it was closed. Under these circumstances, adding nitrogen to Tank E610 would not be expected, and indeed failed, to raise the tank pressure.
The situation at Tank E610 threatened the liquidation plan’s success. With no way to establish at least 14 PSIG pressure inside Tank E610, its contents could not be used for pesticide production. A possible option to feed Tank E610’s inventory out through Tank E611 was excluded when the MIC circulation pump failed during the production run. This untimely event cut off the backdoor leading into Tank E611 through the reject line. Finally, provisions made to send Tank E610’s contents into the production area according to the original process design were defeated years before when the MIC transfer pumps were abandoned due to frequent seal leaks. Since the material inside Tank E610 could not be accessed, attention immediately turned to Tank E611 for production. This kept the liquidation plan on track while buying some time to determine how to handle the situation at Tank E610.
Contamination
Now more than ever, time was of the essence. It was December 2, 1984. Only 29 days remained before the operating license expired and manufacturing would cease.
Tank E611 was almost empty but Tank E610 was still full. Ignoring the situation at Tank E610 could mean that the entire contents of Tank E610 might remain on January 1, 1985. As much as 42 tons of MIC would be wasted at what cost?
An experienced supervisor knew that MIC trimer deposits readily dissolve in water. That was why the water-washing procedure was introduced after the MIC transfer pumps were abandoned, soon after the factory was commissioned in 1979. Routinely flushing debris out of the iron vapor transfer pipes with water kept MIC production quality on-spec after continuous PVH nitrogen flow was interrupted. It also reversed “operating environment” related equipment malfunctions such as Tank E610’s vent valve failure when MIC production was discontinued. The water-washing procedure was an example of making creative use of reality.
Accordingly, supervision gave one of the temporary operators from the battery factory a handwritten diagram showing how to flush debris out of Tank E610’s vent valve by making a water hose connection. This targeted flushing procedure would clear the vent valve of any deposits accumulated during the extended MIC production run. A more invasive approach might be necessary if production from Tank E610 was not restored by flushing the valve out with water, but this was not expected. The recovery procedure was very simple: Introduce water flow through the vent valve for a few hours, close the valve, introduce nitrogen, then establish 14 PSIG inside the tank to confirm that the valve was clean. Afterward, Tank E610’s contents would be used to produce pesticide with the intent to consume the entire inventory within Tanks E610 and E611 before January 1, 1985.
The water-washing procedure was expected to work. It was considered normal practice at this point in the factory’s history, even though the process was not originally designed to accommodate water injection. Furthermore, it was considered safe since it did not require breaking apart connections that could expose workers to toxic materials.
Following instructions provided, the operator closed the “common valve” on Tank E610’s vapor manifold. This action was expected to isolate the tank from the maintenance he was about to perform. He then unscrewed the pressure gauge downstream of the common valve and attached a threaded hose connection. The water hose was attached, and water flow was initiated from a nearby utility station.
Unknown to anyone present at the time this procedure was conducted, the trimer build-up also extended into the iron common valve. Although the operator turned the valve clockwise (closed) until firm resistance was felt, a temporary plug of compressed trimer created an opening. Water therefore passed through the common valve instead of the vent valve, where flow was intended. This hidden failure persisted across the intervening shift; initiating an exothermic reaction inside of Tank E610 that was not noticed until direct signals of an unfolding disaster could not be mistaken.
The operators tried desperately to reverse the situation. They did everything they could, but nothing worked. By then it was too late. The reaction inside Tank E610 had already crossed the point of no return. Unfortunately, time travel is possible only when resurrecting a dead process. Thirty-six years waiting for a disaster to end seems like an eternity.
Note To Self:
Process decisions made in haste end in regret.